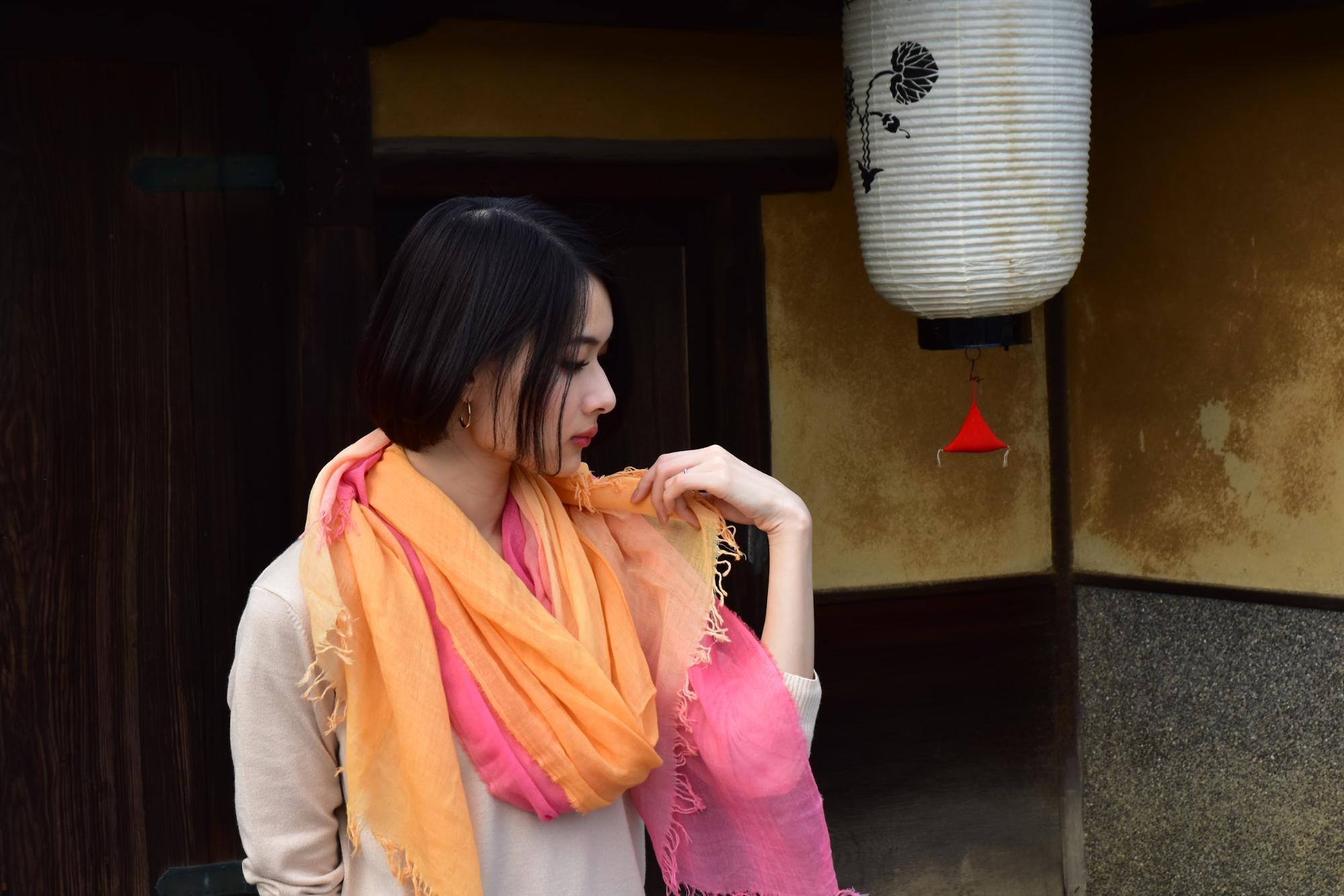
Mari Kozawa 采访,2021 年 2 月 2 日
据称,时尚产业占全球人类活动产生的二氧化碳排放量的10%,并且消耗了全球第二大水资源。此外,诸如拉纳广场(Rana Plaza)坍塌等事件也凸显了时尚界的劳工问题。
鉴于此,寻求有助于缓解环境和劳工问题的“道德时尚”实践的呼声日益高涨。在日本,有一种传统的时尚工艺能够促进时尚的道德规范。草木染,即使用植物和其他天然染料的染色方法,与重视与社会和自然和谐相处的日本传统生活方式相得益彰。草木染在日本自古以来就广为流传,已成为日常生活的一部分。
我参观了京都川端商店举办的研讨会。这家公司在京都,采用拥有1500年历史的草剌染工艺进行制作。我在那里了解了这家公司,并采访了社长川端康夫,了解他与学生们合作的一个项目。
使用1500年前的真万染方法生产道德产品
京都川端商店最初成立于1924年,最初是一家和服公司。该公司于1995年停止经营和服,但仍使用当时尚不常见的石油基染料进行纺织品印染。然而,一些员工因接触化学染料而出现皮肤问题,或因染料气味而头痛。社长川端康夫第一次想到使用天然染料的可能性,是在与员工交谈并寻求解决方案时。
使用石油基染料进行印花是一种相对简单高效且无需专业技能的方法。然而,它也会对环境和人类健康产生显著的负面影响。15年前,川端先生大胆尝试,与三重大学名誉教授木村光夫先生共同研发了一种草木染法。最终,一种名为“新万叶染”的染色方法应运而生,它使用植物和昆虫等天然原料。例如,用万寿菊染黄色,用胭脂虫染粉色,用苏木染浅蓝色,可以染出鲜艳的色彩。京都川端商店出售用新万叶染法染色的披肩。
新万叶染的特点是所需时间和染料最少,而且染色时无需加热。开发新万叶染并改用草木染后,取得了良好的效果,例如能够染出使用合成染料无法染出的绚丽色彩。此外,由于染色液和媒染液都能回归自然,工厂的空气气味也得到了改善,废水也变得更环保。
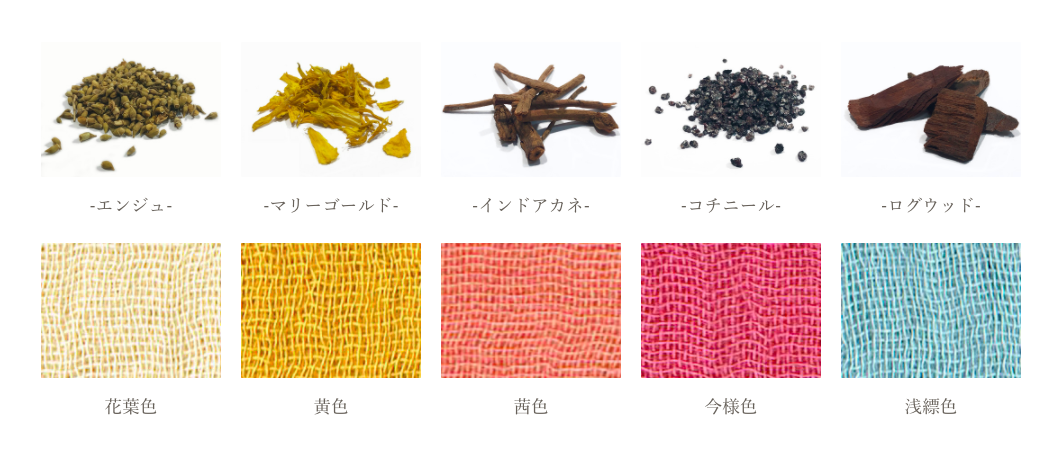
图片来自京都川端书店 - 从左到右:槐树(灰白色)、万寿菊(黄色)、茜草(茜草)、胭脂虫红(粉色)、苏木(浅蓝色)
古老而又新颖的“新万叶染”成为解决污水问题的关键
新万叶染的研发源于川端先生对草木染的兴趣,据说这种染法早在1500多年前就传入日本。与此同时,共同开发该染法的木村博士也对“奈良时代(710-784)的纺织品和纤维是如何染色的”感到好奇。木村博士感兴趣的是研究在没有现代加热设备的时代,如何进行染色,因为当时溶液温度很难超过100摄氏度。(新万叶染的字面意思是“新的万叶染料”,取自七八世纪著名的诗歌选集《万叶》) 万叶集)
此外,在新万叶染的开发过程中,环境污染问题日益受到重视。当时,京都川端商店正在进行丝网印刷(一种在纺织品上印制图案的印刷方法),并面临着废弃油墨和废水处理的问题。为了解决这些问题,他们借鉴新万叶染工艺,开发了一种名为“e 印刷”的新型印刷方法。e 印刷不使用石油基或合成染料,而是仅使用天然颜料在 T 恤等产品上进行印刷。包括辅助材料在内的所有成分均由天然成分制成,因此废水排放后可以回归自然。最终,他们将 e 印刷开发过程中的发现应用于改善新万叶染工艺的显色和废水质量。
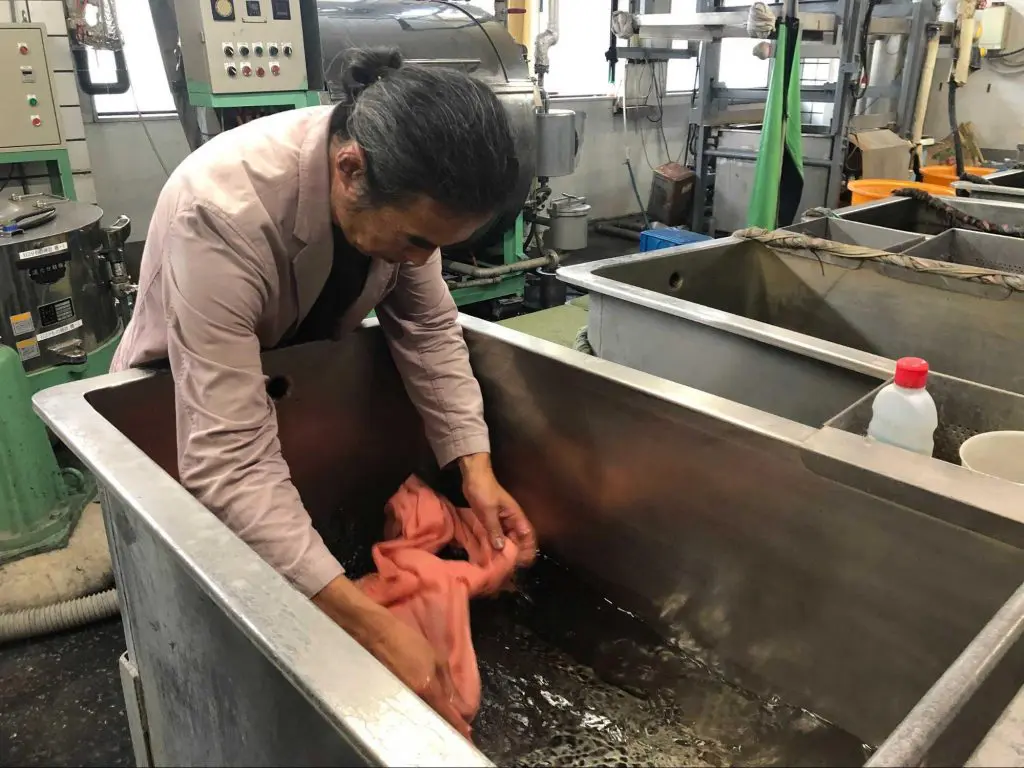
摄影:Mari Kozawa
将重新发现的道德染色方法传承给下一代
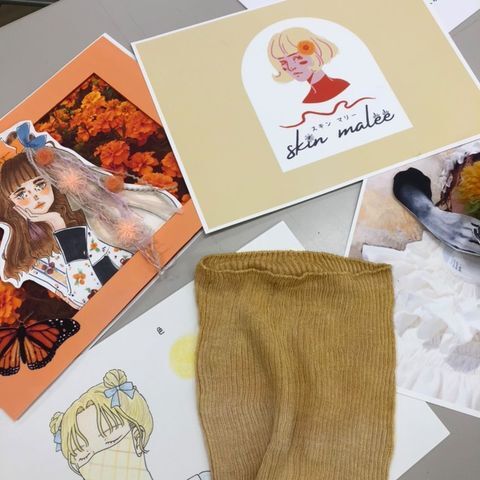
摄影:Yumi Komori
2020年秋季,京都川端商店与京都和大阪的时尚学校合作开展了一项合作项目。学生们根据可持续发展目标(SDGs)中设定的普遍目标:“目标12:确保可持续的消费和生产模式”和“目标17:加强执行手段,重振全球可持续发展伙伴关系”,采摘了原本计划丢弃的有机种植万寿菊。之后,学生们将万寿菊干燥后制成染料,并利用这些染料制作了各自的作品。该项目让生产者、销售者和年轻人共同参与,将日本传统技术与符合道德的时尚联系起来。
未来服装行业不仅重视效率,更重视道德
在了解了该公司的情况后,我采访了京都川端商店的总裁川端康夫先生,了解他与时尚学校合作的项目。
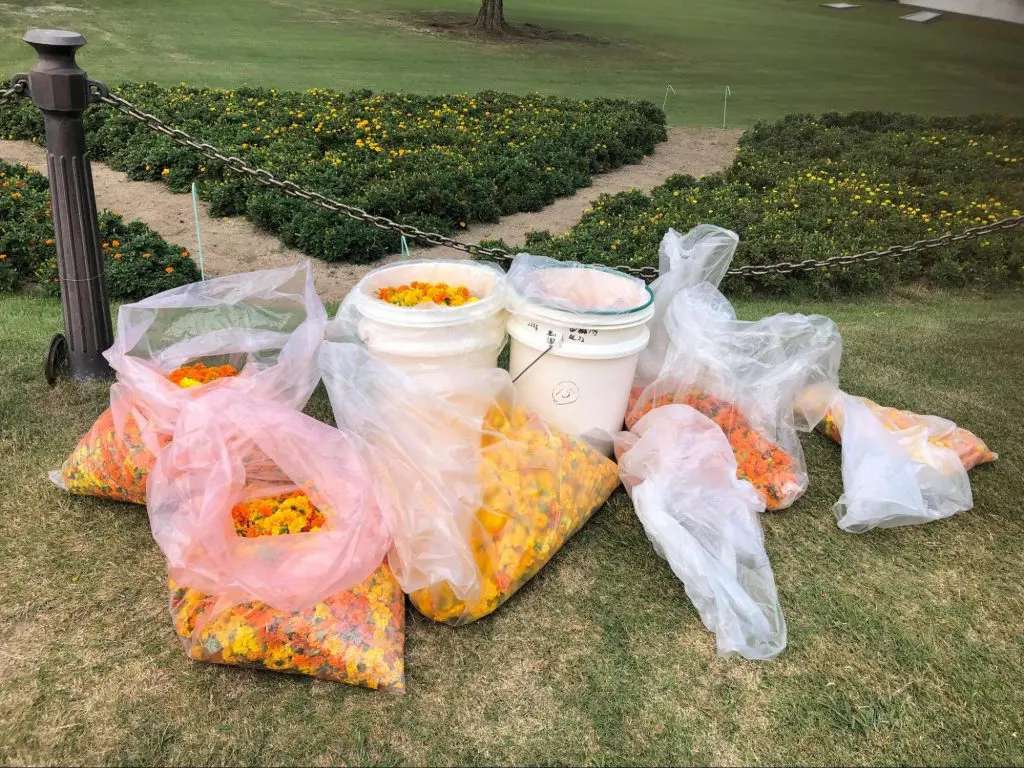
摄影:Yumi Komori
是什么促使您发起这个项目?
2019年,一场强台风摧毁了等待采摘的万寿菊,我们不得不采取紧急措施,设法获取这些材料。我们联系了大阪的植物园和公园,说:“如果您有打算丢弃的万寿菊,请允许我们处理。” 我还解释了我们的动机,说:“我们会将这些废弃物重新用于染色,这都是大自然的馈赠。” 之后,大阪万博纪念公园批准了我们,并指定了采摘日期。之后,我咨询了马罗尼耶服装设计学院和上田服装设计学院,这个项目就这样启动了。
最近,大型服装公司开始表示支持道德时尚和可持续发展目标,但我一直担心学校里缺乏能够讲解这些主题的教师。我预计日本传统服装公司的业务将大幅下滑。“新万叶染”是一种超越传统草咲染的创新方法。在策划这个项目时,我也希望让学生们有机会了解木村博士利用古代技术线索发明的这项新技术。
你觉得和学生们一起做这个项目怎么样?在和他们交流的过程中,你有什么想法吗?
与学生们一起进行的收获过程非常顺利和迅速,我认为品牌推广也朝着好的方向发展,所以我看到了商品化的潜力。虽然这是我们的第一次尝试,最终并没有真正合作生产商品,但我觉得它可以成为产官学合作可持续实践的典范。这项倡议让我在这方面感到充满希望。
而且,我觉得通过这个项目,我传播了环保生产的理念。无论是否在时尚行业,学生们肯定都会在一个不断追求效率的环境中工作。我相信,即使在这样的环境下,时尚界也很快就会出现选择道德生产并切实践行的先驱者。
作者后记
聆听新万叶染方法背后的故事,川端先生为解决员工健康问题和废水问题而采取的热情态度,以及他对道德染色方法的追求,都给我留下了深刻的印象。
我还认为,探索和传承自古以来传承的传统技艺,或许是思考道德时尚未来的重要途径。回顾历史,我们总是用当地现有的材料来制作日常生活用品。在生活环境中进行生产,自然而然地让我们与社区中的其他人以及自然环境建立了联系。
现代生活中,由于追求效率而导致的大规模分工,与他人和自然关系的缺失,或许正是近期浮现的种种社会问题的根源。由于我们缺乏对生产循环以及自身与循环关系的清晰认知,不知不觉中就对环境和劳动者造成了伤害。
工业界的“伦理”概念听起来可能像是一个全新的领域,但事实上,理解代代相传的文化传统或许才是迈出的第一步。正如谚语所说:“欲知后事,必先思过往事。” 或许,寻求传统的本土专业知识,以找到鼓励未来伦理生产的答案,是一个好主意。
参考文献(日语):
京都川端商店“新万叶染简介”
伊藤惠 (Megumi Ito) 编辑
关于作者:Mari Kozawa
TSUNAGU 总监。2018 年加入道德时尚品牌 TSU.NA.GU.,通过设计商业模式并促进生产者和消费者之间的双向沟通,提升时尚的透明度。她还策划并运营与 Z 世代相关的项目,致力于推动社会公益。
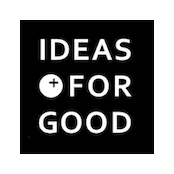